Rods
The initial step in my design process was to determine which materials and concepts from the previous iteration should be retained. A key decision was to repurpose the square, hollow aluminum rods, measuring 2x2 inches, as the main structural components of the frame. Made from 6061 aluminum, these rods offer an excellent combination of properties, making them ideal for the application. With a density of approximately 2.7 g/cm³, 6061 aluminum ensures the frame remains lightweight. Its tensile strength of up to 310 MPa and yield strength of 276 MPa provide outstanding durability, allowing it to withstand significant stresses without deformation. Additionally, with a modulus of elasticity of about 69 GPa, this material offers the necessary elasticity to effectively absorb dynamic loads. These qualities ensure the rods maintain the structural integrity of the frame while contributing to a lighter, more practical design. These rods will also be shorter in this deisgn as to make the robot more lighter.
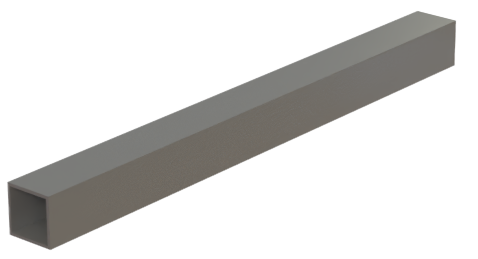
Body Plates
The frame plates of the robot dog are designed to be constructed from acrylic, chosen for its excellent mechanical properties, its affordability, and ease of manufacturing. Acrylic offers sufficient stiffness and strength for the application, with a tensile strength of approximately 70 MPa and a lightweight structure that nicely complements the aluminum frame. This material was also chosen, as we had already selected laser cutting to be our main manufacturing method due to its precision, speed, and availability, making it significantly easier than machining or 3D printing other materials. The design consists of three plates: a front plate, a back plate, and a middle plate. Both the front and back plates feature circular cutouts to house two motors each, facilitating direct attachment to the robot’s legs. The middle plate, while identical in other respects, lacks these cutouts, serving as a structural component to provide additional rigidity and stability to the frame. The following images show the CAD of the front/back plate and its mechanical drawing.
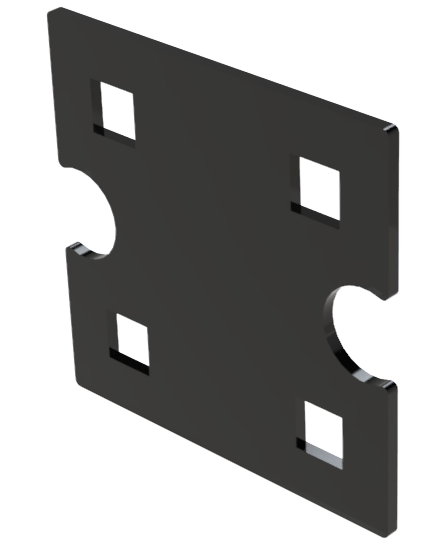

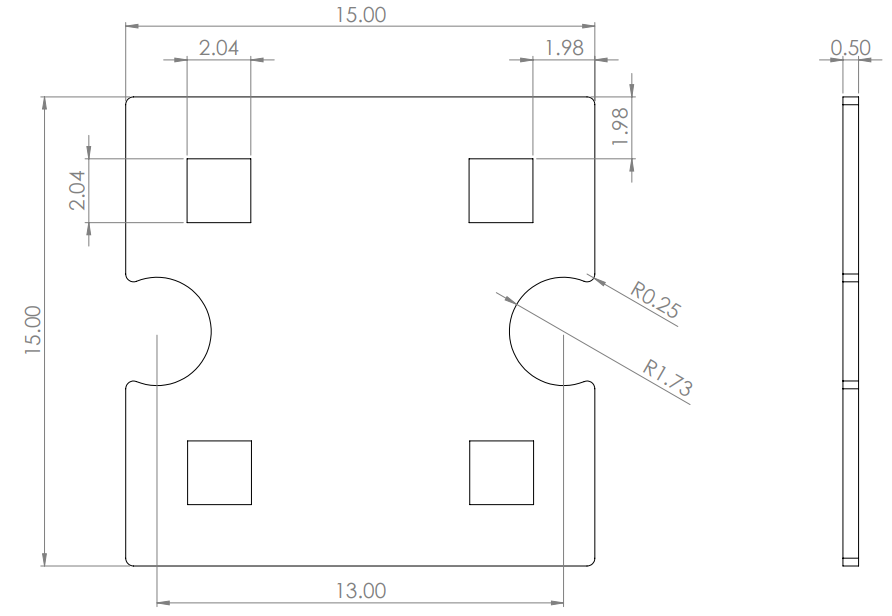
To secure the acrylic plates firmly to the frame, aluminum brackets are employed as a fastening solution. These brackets are designed to fit snugly over the square aluminum rods, and screws are used to tighten the brackets, ensuring that the acrylic plates remain securely in place during the robot’s operation. This fastening method ensures precise alignment of the plates, enhances the overall structural integrity of the frame, and allows for easy assembly and disassembly of this frame, without the need to glue of solder the parts.
LiDAR Sensor Holder
For navigation, a 3D LiDAR sensor will be mounted on top of the robot frame using a custom-designed holder. The holder will be 3D-printed from PLA for its lightweight and durable characteristics, and it is designed to be securely screwed into the top of the middle acrylic plate. To attach the LiDAR sensor, threaded inserts will be embedded in the PLA holder, allowing screws to align with the sensor's mounting holes. This setup ensures a strong connection while enabling easy removal and adjustments for the sensor. The holder’s design also ensures the LiDAR has an unobstructed field of view during navigation.